Heat Treatment of Nitinol for Different Stylet Shapes
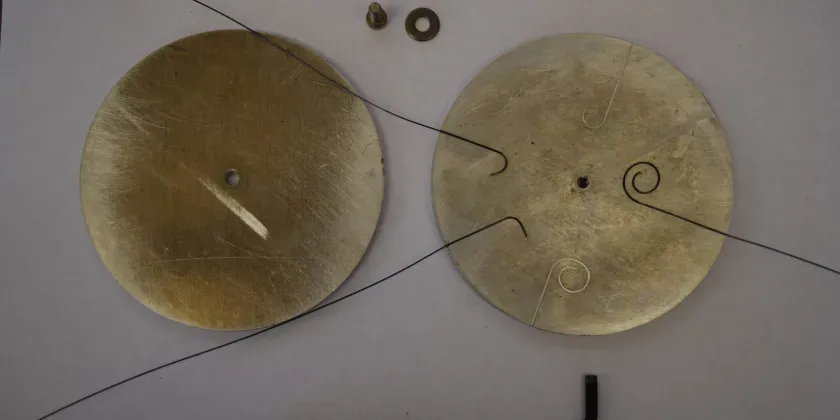
In this post you will learn about an approach to fabricate different stylet shapes for our proposed stylet and tube steerable needles using heat treatment of the Nitinol (a Shape Memory Alloy SMA).
Our lab developed a new class of steerable needles called Stylet and Tube Steerable Needles in which the direction of the tissue fracture is controlled by the inner Stylet followed by the outer tube to help steer the needle.

The shape of the stylet and the step length determine the radius of curvature of the steerable needle. For this reason, we have developed a method based on heat treatment of the Nitinol to make different shapes for the stylet and thus achieve different radii of curvature.
The contributors to this project are Fan Yang, and Mahdieh Babaiasl, under the supervision of Dr. John Swensen.
Procedure for Heat Treatment of Nitinol Wires to Obtain Different Stylet Shapes
To fabricate the optimal shape for each Nitinol stylet geometry, straight Nitinol pieces are pressed in an aluminum mold, heated to 500 C for 30 min, then quenched with water. Five stylet geometries are obtained after heat treatment.
The figures below show the step-by-step process to obtain different stylet shapes:






The same approach can be used to produce Nitinol wires with different pre-curvatures:

You can learn more about the Stylet and Tube Steerable Needles in the links below: